As of May 28, 2025, the Rapid Mixer Granulator (RMG) remains a cornerstone in pharmaceutical manufacturing. This equipment ensures efficient mixing and granulation, enhancing drug production quality. Let’s explore its role in modern solid dosage form development.
Why RMG Is a Game-Changer in Drug Production
In pharmaceutical manufacturing, the Rapid Mixer Granulator (RMG) enhances efficiency in solid dosage production. It ensures uniform mixing and granulation, streamlining the granulation process. Let’s explore its components, process, and benefits for modern drug production.
What Is a Rapid Mixer Granulator?
Understanding the Equipment
A Rapid Mixer Granulator (RMG) is a key machine in pharmaceutical manufacturing. It mixes and granulates powders rapidly, ensuring uniform granules for tablets and capsules. This improves drug quality and production efficiency in solid dosage forms.
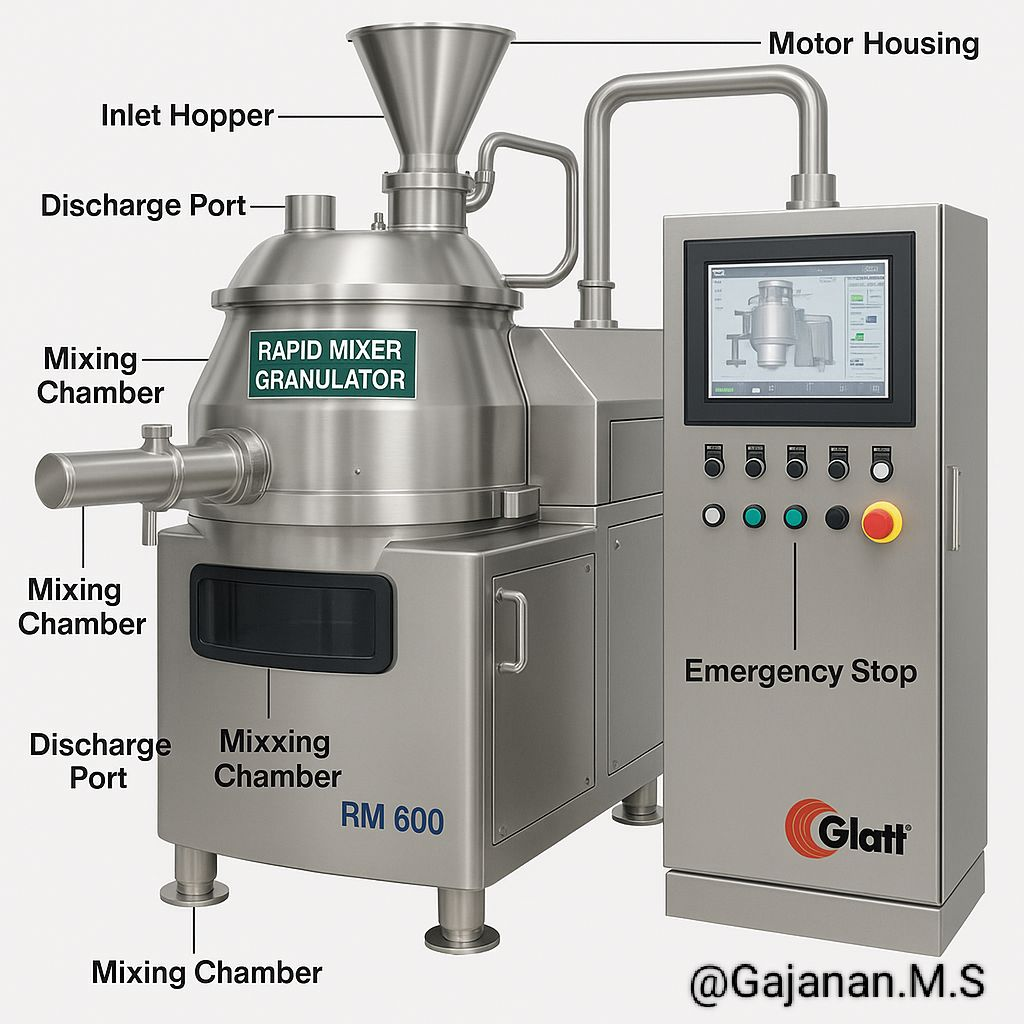
Source: Rapid Mixer Granulator (RMG)
Key Components of RMG
Breaking Down the Machine
- Inlet Hopper: Feeds raw materials into the mixing chamber.
- Mixing Chamber: Houses impeller and chopper for blending.
- Discharge Port: Transfers wet granules for drying.
- Motor Housing: Powers the granulation process.
- Emergency Stop: Ensures safety during operation.
The RMG Granulation Process
Steps for Efficient Drug Production
- Dry Mixing: Blends APIs and excipients evenly.
- Granulation: Adds binder solution, forming wet granules.
- Wet Milling (Optional): Breaks down oversized granules.
- Discharge: Moves wet mass to a Fluid Bed Dryer for drying.
Benefits of RMG in Pharmaceutical Manufacturing
Why It’s Essential for Drug Development
- Uniform Mixing: Ensures consistent API and excipient blending.
- Granule Control: Achieves optimal size for tablet compression.
- Time Efficiency: Shortens batch cycles, boosting productivity.
- Regulatory Compliance: Meets cGMP and FDA standards with hygienic design.
Why RMG Matters in Pharma
Driving Quality and Efficiency
RMG is vital for speed-to-market and quality assurance in drug production. It minimizes errors, optimizes resources, and ensures batch consistency. For more on granulation processes, visit USP for industry standards and insights.
Frequently Asked Questions (FAQs)
What is the purpose of an RMG in pharmaceutical manufacturing?
An RMG mixes and granulates powders to create uniform granules for tablets and capsules. It ensures consistent drug quality and improves production efficiency in pharmaceutical manufacturing processes.
How does the RMG granulation process work?
The RMG process involves dry mixing APIs and excipients, adding a binder for granulation, optional wet milling, and discharging the wet mass to a dryer. This ensures uniform granules for drug production.
What are the main benefits of using an RMG?
RMG offers uniform mixing, consistent granule size, time-efficient batch cycles, and compliance with cGMP and FDA standards. It enhances quality and productivity in pharmaceutical manufacturing.
Is the RMG suitable for all types of drugs?
RMG is ideal for solid dosage forms like tablets and capsules. It’s less suited for liquid or semi-solid formulations, where other equipment may be more appropriate.